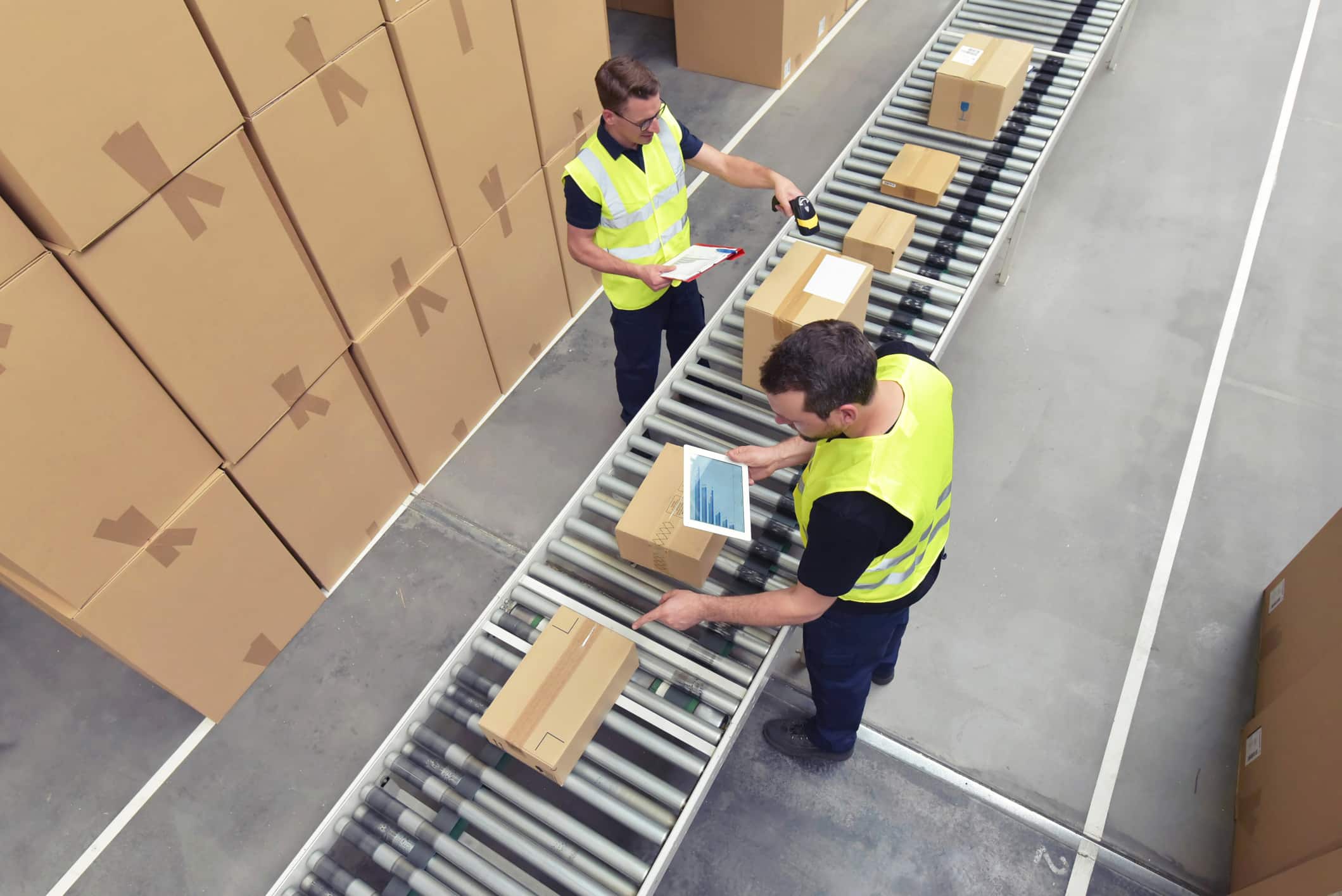
If we look at the big picture, the UK logistics industry has good reason to be optimistic. Inflation is cooling, energy costs seem to have stabilised and supply chain issues have abated. The latest Barclays Logistics Confidence index confirms this, with the sector agreeing that things are now moving in the right direction after a tricky couple of years.
There’s a caveat here though; at the day-to-day level, many key challenges remain. While those challenges span everything from operations to orders, AI to fleet management — access to a flexible workforce could unlock a range of benefits which are similarly broad in scope.
Unpacking the underlying causes for concern
Around half of logistics firms say that business conditions are tougher today than they were a year ago. Much of that sentiment stems from the growing cost of being in business, ongoing staffing shortages and changing business volumes.
1. Price pressures
When it comes to the biggest challenges likely to shape the next 12 months, 68% of logistics leaders cite price pressures as their greatest cause for concern. There’s a perfect storm brewing, with rising costs for essentials like fuel, energy and staff coming at a time when customers are pushing for better value and lower contract pricing.
2. Fluctuating demand
50% of logistics firms say they expect fluctuating demand to be a major issue throughout 2025. As UK shoppers continue to feel the pinch of the cost of living crisis, retail sales are declining – but this trend is expected to change as we move into summer.
3. Staff shortages
38% of logistics businesses say staff shortages and increased labour costs will be their biggest challenge. There are 128,000 fewer EU workers in transport and warehousing since Brexit, leading to a real need for more people on the warehouse floor.
As we reported in 2023, demand for warehouse operatives has spiked to 43% above pre-pandemic levels. Driver shortages are also well documented, with a shortfall of around 30,000 delivery drivers. Toyota estimates the number of qualified forklift truck drivers is around 25% below required levels. These gaps highlight how strategic staffing in logistics can ease the burden.
5 ways a flexible workforce can help logistics businesses to overcome these bumps in the road
1. Staff according to demand
Flexible workforce management allows companies to scale up or down at pace. Matching staffing levels to real-time demand avoids overstaffing during quieter periods and reduces the threat of understaffing if there’s a sudden spike.
2. Cost efficiency
With rising costs being a major pressure point, adopting a flexible staffing model is an easy way to reduce fixed labour costs while remaining compliant with changing regulations. Paying on an as-needed basis can improve overall profitability, which provides a buffer against wider uncertainty.
3. Faster hiring and onboarding
Easy access to a pool of skilled contingent workers enables faster recruitment and onboarding, especially in last-mile delivery and warehouse operative roles. This isn’t just a time and cost saver — it also helps to ensure your productivity and efficiency goals are met.
4. Access to a broader talent pool
Flexible roles appeal to a wide range of workers including students, parents, semi-retired individuals, and gig economy workers.
So flexible staffing in logistics is a smart way to access diverse talent pools and close the skills gap much faster than may otherwise be the case. Crucially, it unlocks access to people not available for full-time roles but who still have the experience needed to cover a picker packer, delivery driver or forklift operator shift.
5. Resilience during disruption
A flexible workforce gives you the freedom to respond more effectively and creatively to unexpected challenges such as supply chain issues, weather disruptions, or driver shortages. It also makes your business more resilient in the face of wider geopolitical uncertainty and changing government legislation.
Ultimately, intelligent staffing in logistics models ensure critical gaps are quickly filled, regardless of the nature of the disruption.
Final thoughts
Challenge and opportunity quite often go hand in hand, and that’s certainly the case for UK logistics today. With rising costs, staff shortages, and swings in demand, the only certainty is that warehouse and logistics businesses must be prepared to pivot at a moment’s notice. Flexible staffing in logistics has never been more beneficial than it is right now. Its scalable nature means that it can alleviate several underlying pressures while also providing plenty of room to manoeuvre as the year progresses.
Subscribe to our newsletter
Stay ahead of employment updates and workforce management tips. Subscribe to our newsletter for expert insights straight to your inbox.